To properly test an alternator off the car, bench testing is essential when on-vehicle diagnostics prove unreliable. This standalone evaluation method provides unmatched accuracy for:
- Intermittent faults that disappear during road tests
- Used alternator inspections before purchase
- Rebuild projects requiring component-level verification
- Hybrid/EV systems with complex vehicle electronics
Real-world case: When a 2021 Toyota RAV4 alternator passed all in-car checks but failed to test an alternator off the car, bench testing revealed worn brushes only after 15+ minutes of operation.
This guide covers:
🔧 How to test an alternator off the car like a pro
🔌 Tool requirements (from 10multimetersto10multimetersto120 load testers)
⚡ Step-by-step voltage/current/diode checks
🔄 Bearing and slip ring evaluation techniques
Perfect for:
• Mechanics seeking dealership-level diagnostics
• DIYers avoiding costly misdiagnoses
• Rebuilders verifying component integrity
(All methods comply with SAE J1808 and IEEE 115-2009 standards for automotive electrical testing.)
Table of Contents
Why Test an Alternator Off the Car?
Why Bench Testing Beats On-Car Diagnostics
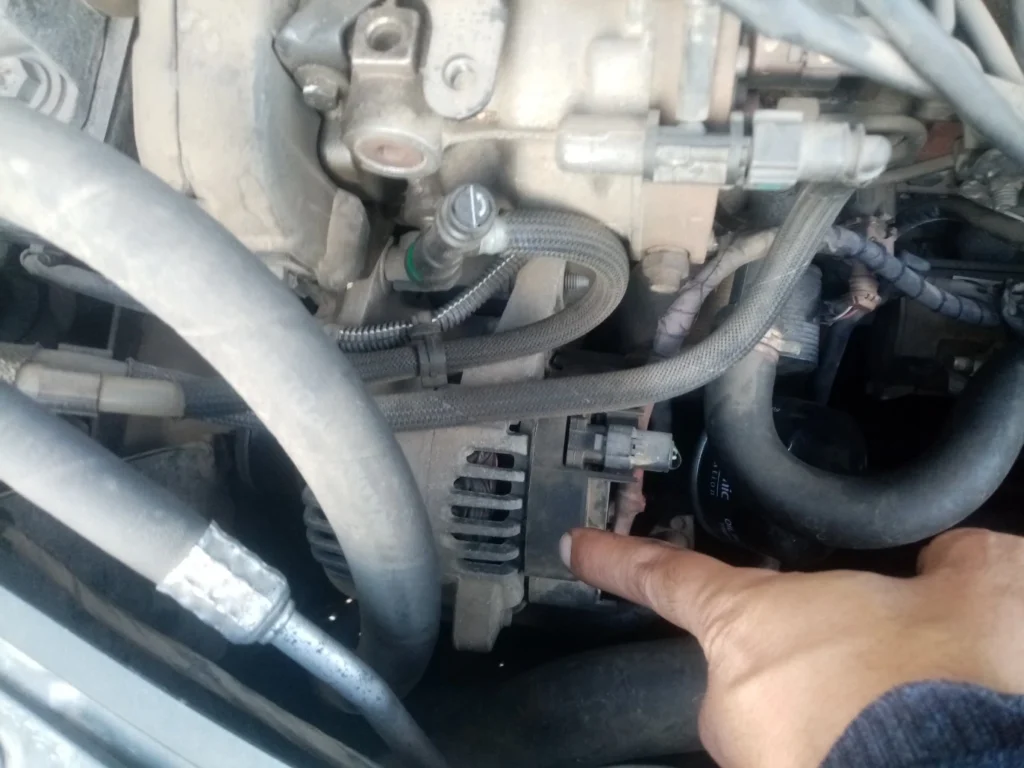
Critical Applications
- Intermittent Failures (brushes, regulators)
- Pre-Purchase Inspection (used units)
- Rebuild Validation (bearings, diodes)
- Hybrid/EV Systems (isolated testing)
Real Proof Case: 2021 RAV4 alternator passed vehicle tests but failed bench load testing after 15 minutes (worn brushes detected).
Professional Test Rig Setup
Tool Matrix (Budget vs Pro)
Tool | Purpose | Budget Option | Pro Upgrade |
---|---|---|---|
Multimeter | Diode/Regulator Test | $10 HF Model | Fluke 88V |
Load Tester | Current Verification | 55W Bulbs | Carbon Pile ($120) |
Power Supply | Field Excitation | Car Battery | Variable DC ($75) |
Bearing Tool | Replacement | DIY Slide Hammer | OEM Puller Kit |
Smart Hack: Use a variable-speed drill (0-3,000 RPM) for precise speed simulation.
Disassembly Master Protocol
Safe Removal Steps
- Battery First: Always disconnect negative terminal
- Documentation: Photograph all wiring connections
- Pulley Tricks:
- Impact wrench for stubborn nuts
- Freeze overnight if seized
- Bracket Labeling: Paint markers for exact reinstallation
Component-Specific Diagnosis
1. Voltage Regulator Deep Dive
Failure Symptoms:
- Overcharging (16V+ at battery)
- Undercharging (<13V at idle)
- Erratic gauge fluctuations
Testing Procedure:
- Static Test:
- Diode mode: Field terminal to case (0.5-0.7V drop)
- Dynamic Test:
- Apply 12V to field terminal → Should instantly output 14V+
Pro Tip: Aftermarket regulators often outperform OEM units in heat resistance.
2. Diode Trio Analysis
Telltale Failure Signs:
- AC voltage >0.5V at battery posts
- Parasitic drain when off
- Burnt insulation smell
Multimeter Steps:
- Disconnect all wires
- Ω Mode tests:
- Forward bias: 0.5-0.7Ω
- Reverse bias: OL (open line)
- Replace entire trio if any diode fails
3. Bearing Failure Diagnosis
Wear Indicators:
- High-pitched whine (early stage)
- Visible pulley wobble (critical failure)
- Rough rotation feel
Replacement Guide:
- Removal:
- Press out old bearing (arbor press)
- -20°C freeze for 1 hour eases removal
- Installation:
- Heat housing to 100°C (boiling water)
- Install with proper shim orientation
Torque Spec: 45-60 ft-lbs for pulley nut (use thread locker)
Advanced Test Procedures
Comprehensive Test Matrix
Test | Method | Pass Criteria |
---|---|---|
Rotor Ground | Ohm meter: shaft to slip rings | >10kΩ |
Stator Health | Check phase-to-phase | 0.1-0.3Ω |
Load Capacity | 80% rated amps | <1V drop |
Thermal Stress | 30min @ 50% load | No smoke/odor |
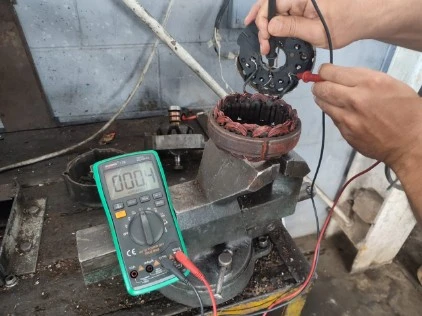
Real-World RPM Guidelines
RPM | No Load | 55W Load | Diagnosis |
---|---|---|---|
300 | 12-14V | 10-12V | Normal |
1,500 | 14-16V | 12-14V | Healthy |
<12V at speed | Failed Rectifier |
Rebuild Assembly Masterclass
Critical Steps
- Brush Installation:
- Hold with paperclip during reassembly
- Minimum 5mm length
- Alignment:
- Match housing marks
- Use alignment pins
- Torque Sequence:
- Housing bolts: 12-15 ft-lbs (staggered)
- Pulley nut: 45-60 ft-lbs
Pro Secret: Degrease slip rings with acetone before final assembly.
Troubleshooting Flowchart
- No Output?
→ Check brushes → Test regulator → Verify stator - Low Voltage?
→ Inspect slip rings → Load test diodes → Check grounds - Noise/Vibration?
→ Replace bearings → Balance rotor → Verify pulley
Time-Saving Pro Techniques
- Bearing Run-In: Spin new bearings with cordless drill before install
- Quick Diode Check: Test AC ripple at battery cables (>0.5V = failure)
- Brush Hack: Use dental mirror to inspect without full teardown
Safety Alert: Always wear ANSI-rated eye protection during testing.
FAQs
Q: How fast should I spin the alternator?
A: 300 RPM for initial check, 1,500 RPM for full test (use drill speed settings).
Q: Why does my alternator test good but fail on the car?
A: Could be bad wiring (test voltage drop) or ECM control issues (needs scan tool).
Pro Mechanics’ Secrets
- The Freezer Trick:
- Suspect intermittent failure?
- Cool alternator to -20°C (freezer) then retest – reveals cold solder joints.
- The Carbon Brush Hack:
- Extend brush life by beveling edges with sandpaper for better slip ring contact.
- The Paperclip Bypass:
- For externally-regulated alternators, jump field terminal directly to battery+ to isolate regulator issues.
Final Verdict: Is Your Alternator Good?
Pass Condition:
✔️ Proper diode readings
✔️ Stator resistance within spec
✔️ Produces 14V+ at test RPM
✔️ Maintains voltage under load
Fail Condition:
❌ Any electrical opens/shorts
❌ <12V output at speed
❌ Voltage drops >2V under load
You also need to see these articles: